Safety relay modules and safety controllers are devices used in the safety-related part of control systems to perform control so that the machine operation is permitted only when safety is confirmed.
Specifically, it checks signals from inputs such as emergency stop switches and interlock switches, determines that it is safe, and controls contactors and other devices connected to outputs based on the results of that determination. In other words, the safety relay module and safety controller play a central role as the logic unit in the safety-related part of the control system (Figure 1).
- Startseite
- Safety relay module / safety controller
Lösungen
Kostenreduzierung
Compact components
Compact components
LED lighting
LED lighting
PLCs
PLCs
PLC/HMI programming suite
PLC/HMI programming suite
Extended-life components
Extended-life components
Kostenreduzierung
Reduzierung des Kohlenstoff-Fußabdrucks
PID controls/ thermal engineering
PID controls/ thermal engineering
Efficient power supply
Efficient power supply
LED lighting
LED lighting
12 VDC PLCs
12 VDC PLCs
Reduzierung des Kohlenstoff-Fußabdrucks
Mehr als nur Sicherheit
Collaborative Safety
Collaborative Safety
Safety 2.0
Safety 2.0
Emergency-stop Safety
Emergency-stop Safety
Machine Safety
Machine Safety
Functional Safety
Functional Safety
Safety Consulting
Safety Consulting
Traceable Systems
Traceable Systems
Mehr als nur Sicherheit
Minimierung von Ausfallzeiten
Long-lasting Durable Devices
Long-lasting Durable Devices
Remote Monitoring and Control
Remote Monitoring and Control
Preventive/Predictive Maintenance
Preventive/Predictive Maintenance
Easy Replacements
Easy Replacements
Avoid Downtime Caused by Accidents
Avoid Downtime Caused by Accidents
Minimierung von Ausfallzeiten
Optimierung der IIoT-Praktiken
Remote monitoring
Remote monitoring
Traceable systems
Traceable systems
Production line safety
Production line safety
Smart inspection
Smart inspection
Optimierung der IIoT-Praktiken
Explosionsschutz
Remote Monitoring
Remote Monitoring
Machine Safety
Machine Safety
Reducing Maintenance
Reducing Maintenance
Traceability
Traceability
Expertise Support
Expertise Support
Explosionsschutz
Arbeitskräftemangel
Applying Robots
Applying Robots
Remote Monitoring and Control
Remote Monitoring and Control
Preventative Maintenance
Preventative Maintenance
Predictive Maintenance
Predictive Maintenance
Automation
Automation
Arbeitskräftemangel
- Kostenreduzierung
- Compact components
- Compact components
- LED lighting
- LED lighting
- PLCs
- PLCs
- PLC/HMI programming suite
- PLC/HMI programming suite
- Extended-life components
- Extended-life components
- Kostenreduzierung
- Reduzierung des Kohlenstoff-Fußabdrucks
- PID controls/ thermal engineering
- PID controls/ thermal engineering
- Efficient power supply
- Efficient power supply
- LED lighting
- LED lighting
- 12 VDC PLCs
- 12 VDC PLCs
- Reduzierung des Kohlenstoff-Fußabdrucks
- Mehr als nur Sicherheit
- Collaborative Safety
- Collaborative Safety
- Safety 2.0
- Safety 2.0
- Emergency-stop Safety
- Emergency-stop Safety
- Machine Safety
- Machine Safety
- Functional Safety
- Functional Safety
- Safety Consulting
- Safety Consulting
- Traceable Systems
- Traceable Systems
- Mehr als nur Sicherheit
- Minimierung von Ausfallzeiten
- Long-lasting Durable Devices
- Long-lasting Durable Devices
- Remote Monitoring and Control
- Remote Monitoring and Control
- Preventive/Predictive Maintenance
- Preventive/Predictive Maintenance
- Easy Replacements
- Easy Replacements
- Avoid Downtime Caused by Accidents
- Avoid Downtime Caused by Accidents
- Minimierung von Ausfallzeiten
- Optimierung der IIoT-Praktiken
- Remote monitoring
- Remote monitoring
- Traceable systems
- Traceable systems
- Production line safety
- Production line safety
- Smart inspection
- Smart inspection
- Optimierung der IIoT-Praktiken
- Explosionsschutz
- Remote Monitoring
- Remote Monitoring
- Machine Safety
- Machine Safety
- Reducing Maintenance
- Reducing Maintenance
- Traceability
- Traceability
- Expertise Support
- Expertise Support
- Explosionsschutz
- Arbeitskräftemangel
- Applying Robots
- Applying Robots
- Remote Monitoring and Control
- Remote Monitoring and Control
- Preventative Maintenance
- Preventative Maintenance
- Predictive Maintenance
- Predictive Maintenance
- Automation
- Automation
- Arbeitskräftemangel
Safety relay module / safety controller | EMEA
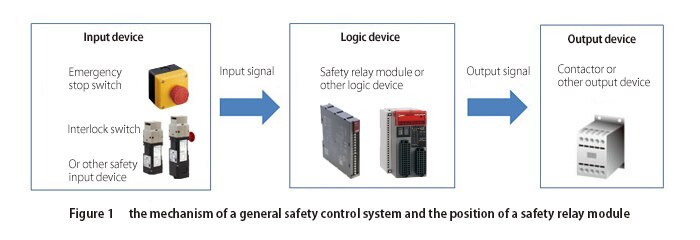
Safety Relay Modules
A typical safety relay module contains several force guided relays and electronic components in an enclosure. It is also designed to be installed inside the control panel.(e.g. on a DIN rail)
Function of Safety Relay Modules / Safety Controllers in the Safety-related Part of a Control System
To start, the overall function of the safety-related part of the control system will be explained. As an example, we use a system with a safety function where a contactor opens and closes the load (motor) circuit in response to operation of an emergency stop switch (Figure 2). If the emergency stop switch is pressed while the motor is running, the motor is stopped immediately.
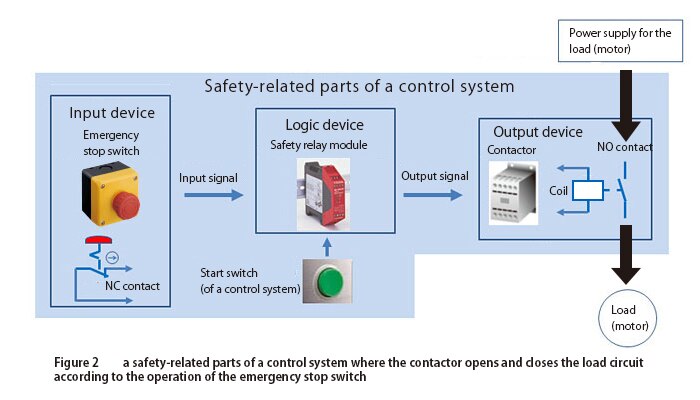
Emergency stop switches use NC (normally closed) contacts, which are normally closed (turned on) and output a signal (safety signal) that indicates a safe state. On the other hand, if some problem occurs and an emergency stop switch is used (pressed), the NC contact opens (turns off), and the safety signal is no longer output.
The safety relay module / safety controller outputs a signal to the contactor that permits the motor to run when the safety signal from the emergency stop switch has been input and the start (activation) switch of the control system has been pressed. When the contactor contacts are closed (turned on) and power is supplied from the power supply, the motor will start running. Note that the contactor contacts are NO (normally open) and are open (off) when there is no signal from the safety relay module.
In this type of safety control system, if the emergency stop switch is pressed while the motor is running, the safety signal is no longer input to the safety relay module, and the safety relay module stops outputting the signal to the contactor (the signal that allows the motor to run). In response, the NO contact of the contactor shall also open (turn off), and the motor shall stop.
Furthermore, when the emergency stop switch is pressed, even if the start switch is pressed, the safety relay module shall not output a signal (to allow the motor to run) to the contactor, and so the motor shall not run. To restart the motor, the emergency stop switch shall be reset (released from the activated state), and then the start switch shall be pressed separately.
The safety relay module / safety controller outputs a signal to the contactor that permits the motor to run when the safety signal from the emergency stop switch has been input and the start (activation) switch of the control system has been pressed. When the contactor contacts are closed (turned on) and power is supplied from the power supply, the motor will start running. Note that the contactor contacts are NO (normally open) and are open (off) when there is no signal from the safety relay module.
In this type of safety control system, if the emergency stop switch is pressed while the motor is running, the safety signal is no longer input to the safety relay module, and the safety relay module stops outputting the signal to the contactor (the signal that allows the motor to run). In response, the NO contact of the contactor shall also open (turn off), and the motor shall stop.
Furthermore, when the emergency stop switch is pressed, even if the start switch is pressed, the safety relay module shall not output a signal (to allow the motor to run) to the contactor, and so the motor shall not run. To restart the motor, the emergency stop switch shall be reset (released from the activated state), and then the start switch shall be pressed separately.
Safety Controllers
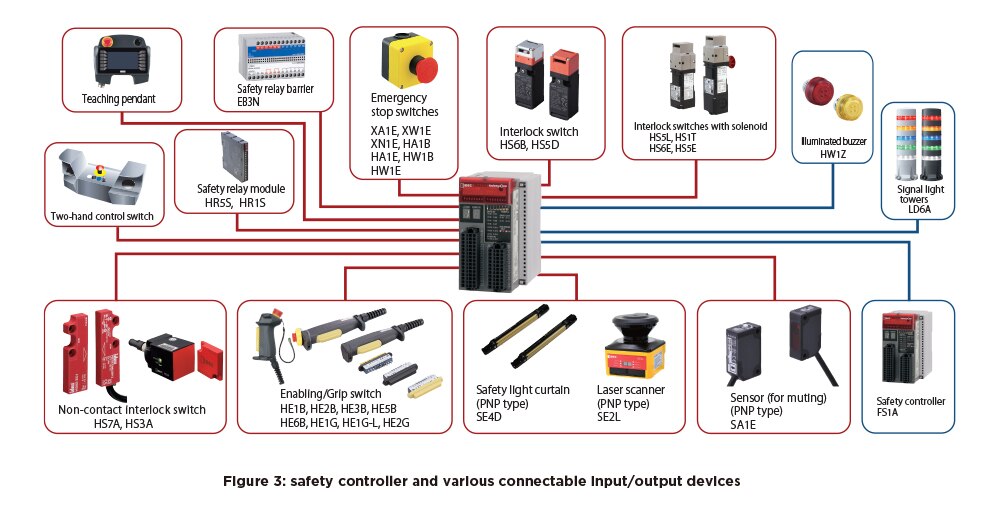
The safety controller is a safety device that, like the safety relay module, serves as the logic unit in the safety-related part of a control system.
As machines become more sophisticated and various safety devices are introduced, the safety-related part of control systems will continue to grow in complexity. The safety controller can be said to be a device that combines high safety performance with ease of use because the CPU functions can be used to easily set up the logic processing and combinations of various safety devices needed to ensure machine safety (Figure 3).
As machines become more sophisticated and various safety devices are introduced, the safety-related part of control systems will continue to grow in complexity. The safety controller can be said to be a device that combines high safety performance with ease of use because the CPU functions can be used to easily set up the logic processing and combinations of various safety devices needed to ensure machine safety (Figure 3).